Projects
Inside Balmoral’s new state of the art subsea facility
A brand new, £20m subsea test centre has been launched in Aberdeen by offshore engineering specialists Balmoral. The company’s engineering and projects director, Fraser Milne, speaks to Molly Lempriere about the challenges of constructing the centre
P
rince Charles officially launched the new Balmoral subsea test centre in Aberdeen in October last year. Over 100 people attended the event in Loirston, as the £20m test centre opened its doors for the first time. It was constructed in less than two years and includes 23 pressure vessels, a 40t lifting crane and bespoke remote monitoring software.
The centre will allow oil and gas companies to test out a whole range of technologies, in particular facilitating pressure valves and other equipment essential to the growing deepwater market. The new centre, which Prince Charles described as a “wonderful example” of innovation, can now provide independent testing of subsea equipment to 7,000msw equivalent.
The testing facility should create a centre of excellence for Aberdeen, as Balmoral’s engineering and projects director Fraser Milne explains.
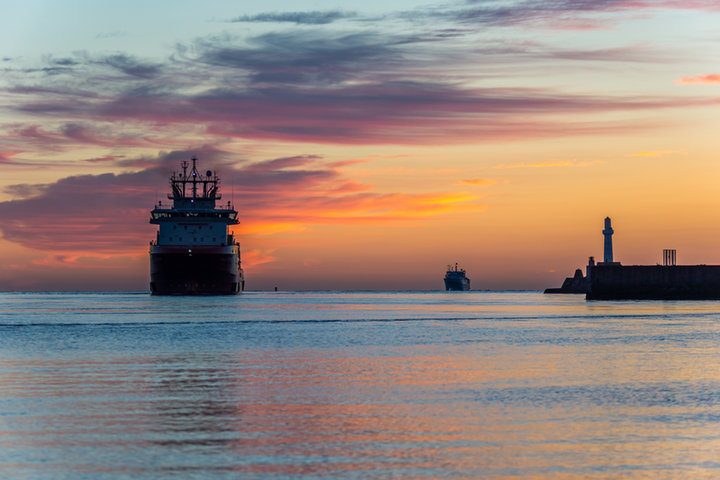
Aberdeen Harbour
Molly Lempriere: What sort of facilities are there in the new test centre?
Fraser Milne: In the new test centre there are 23 pressure vessels. They go down to about 5,000m, and we do have some smaller vessels. We have various pressure vessels for all depths and all sizes of products.
Mostly these carry out performance testing; we get a lot of sub-contractors coming in with products that are going down to the seabed. They want to put them under the same operating pressures that they're going to see in service, and ensure that their product performs as expected and there are no unforeseen leaks.
Some of them are electrical products, and they want to see if water can get into the electrics and make the products fail. So they want to make sure that everything that goes into the sea is going to work first time.
You've designed bespoke software as part of the test centre. Could you tell me a little bit about that?
One of the issues that we had in the test centre was that you want to be able to track everything. In the olden days there were no recorders on every pressure vessel, or manual recording instruments at every pressure vessel. So what we decided was that we want to get away from all that old technology and build bespoke software that would monitor the vessels, monitor pressure, temperature, time of the products going in.
When they're under test, technologies can be monitored from anywhere in the world from a data access portal, as well as it going onto digital screens within the factory. These allow you to see in real time if there's anything going wrong within the pressure vessel of a customer’s product or even one of our products. I can even monitor what's going on in the pressure vessels from home on my iPhone, which is something new.
Predominantly the software uses the Internet of Things, but we used a local contractor called Codify who are a software design house within Aberdeen. It was a collaboration with them to design the software, and then there was another company that did all the background controls that actually run the vessels.
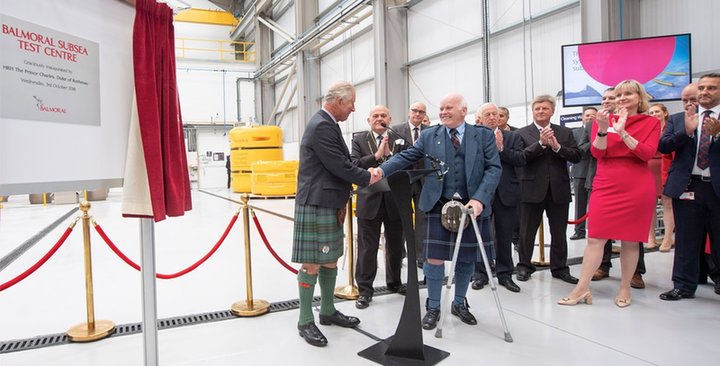
Credit: Balmoral Offshore
It was built in less than two years, which seems like a phenomenally short period of time. Were there any particular challenges surrounding the construction?
Yes, some huge challenges. Aberdeen is named the Granite City, because the whole town is built on granite. When we're trying to drill 50m into the ground we're going into 50m of granite, so we had to use a significant amount of explosives to displace the granite and allow us to put the vessels in.
Drilling these holes would have been possible in the past, but without the level of control needed. What you have to remember is that we built this facility in close proximity to all the other factories. So when we're talking about using dynamite to blow holes, you can picture a wild explosion, but it's all very precise, very controlled, which allows us to build the facility and the holes within close proximity to the other buildings without any risk to their personnel or equipment.
One of the other challenges we had was putting the pressure vessel into the facility. It was actually the biggest load that's ever been brought into Aberdeen Harbour and taken across the river. It was quite interesting; over the river in Aberdeen there are two bridges, one new one and one that's 300 years old. The new bridge couldn't take the load, so the pressure vessels had to come over the old bridge.
We hired Macintosh Heavy Logistics, who got awarded a transport award for the moving and lifting operation in the end, and the operation happened overnight. They had to put the vessel up in the dark. Pretty much driving through the city centre on the wrong side of the road so it could get through the city.
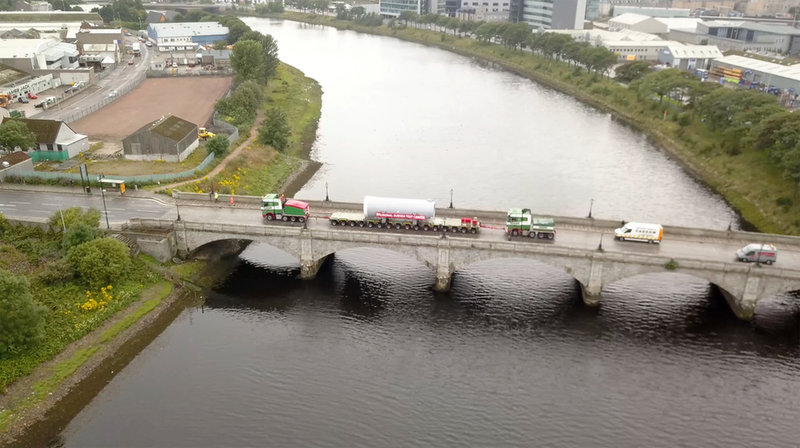
Pressure vessels crossing the old bridge. Credit: Balmoral Offshore
Can you tell me a little about any of the tests that the centre has planned for the future?
The main focus of the test centre for the future is to support the oil and gas industry with control panels, control valves, pressure valves, that we'll be testing for our customers.
For ourselves, it gives us the opportunity to test our products deeper and longer. One of the problems that we've had in the past when we were limited to three or four pressure vessels, if you put a product under test for three/four/five months, it becomes a bottleneck on your production. Now that there are 23 vessels we can put product samples on test for long periods of time without impacting their capacity.
The oil and gas industry has moved towards deepwater, which traditionally has been about 2,000m-3,000m. But what we’re seeing now, is that there's a real drive towards 4,000m and 4km under the sea is quite deep. And that's brought in a lot of development.
Our expertise has always been deepwater, which is why we've always had to have pressure vessels for our own products. But what we're doing now, we're developing products for 4,000m/5,000m and beyond. This test centre is allowing us to do that for our own products and then we'll help others who will have the same challenges as we have.
How do you expect demand at the centre to change given the changing nature of the industry?
What we've seen with oil and gas is there's been a real focus on making sure products work first time and that there's no risk. What a lot of people use the test centre for is to de-risk products for when they go into service.
Although decommissioning is growing, on that side there's probably less involvement from test centres because the products that are being decommissioned are at the end of their 25 years. But there are still people looking at technologies around this and we've actually got interest from one company that is heavily involved in decommissioning. They're going to put in an abandoned well monitoring system, and they're going to do trials of this monitoring system within one of our pressure vessels, and this is testing for months at a time, to ensure that once it goes into the sea that it will actually work.
We're also seeing a lot of interest in the vessels from the defence industry for defence products, we're seeing oceanographic. We've had some students in recently testing ROVs and such like.
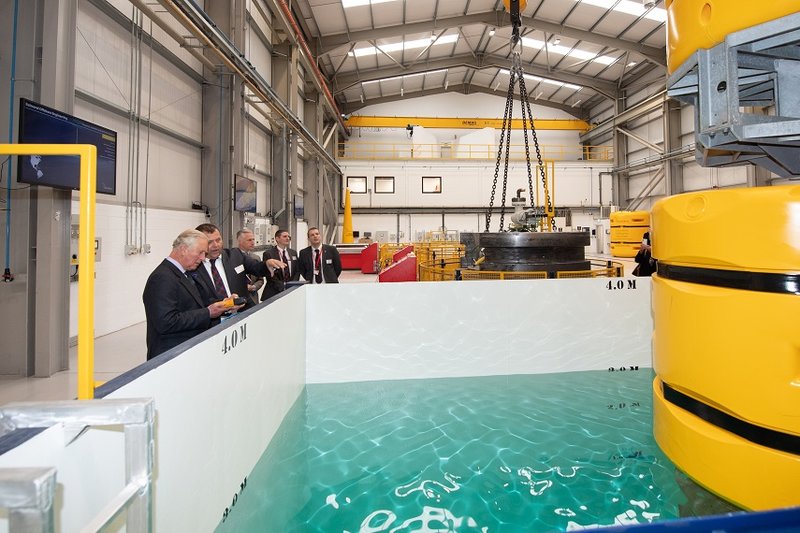
Opening of the Balmoral subsea centre. Credit: Balmoral Offshore
How important do you think the centre will be for the economy in Aberdeen and for Scotland?
We hope it brings a centre of excellence to Aberdeen; these facilities haven't been available within Aberdeen before. We always had a facility to test our products but it was very much limited to our products and what we're hoping to do is open up that to everyone else so that people who are putting out valves and putting out everything else in Aberdeen, has a local place, they don't have to ship it around the world.
There are other facilities in places like Houston, but you don't want to be shipping from Aberdeen to Houston just to check your product. You'll now be able to check your product in Aberdeen and be able to deliver it far quicker.
We're also hopeful that we'll bring in products from further afield, there are other facilities like ours around the world but they're a lot smaller and their capabilities are a lot smaller, so we're hoping that we'll be able to bring in some customers from the likes of Norway and other areas.