Interview
How will digital twins recreate oil and gas?
Digital twins can replicate physical facilities in a virtual world, but what are the real benefits beyond the technology? Elliot Gardner speaks to Honeywell’s Manas Dutta.
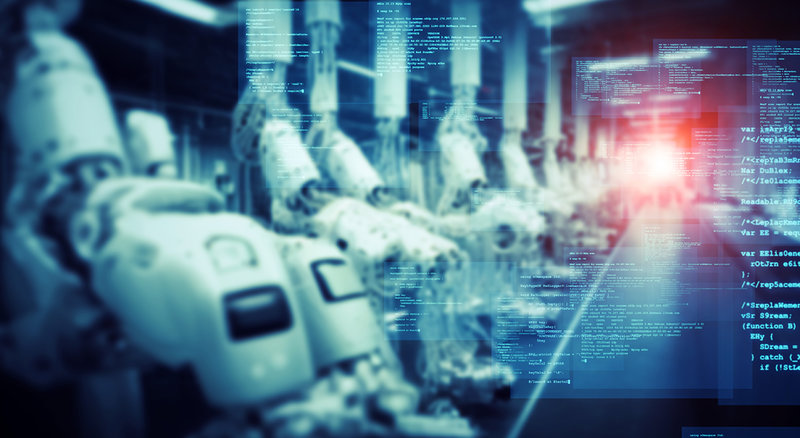
Recreating physical spaces in cyberspace. Credit: Metamorworks via Shutterstock
Digital twins are already rocking the energy sector, offering virtual representations of grids that can help utility companies improve planning and offer significant efficiency benefits, delivering huge time and cost savings for providers across entire energy networks. The oil & gas space has traditionally lagged behind somewhat, but a series of digital twin and metaverse investments from giants of the sector has propelled this technology forward significantly in recent years.
But while other industries have imagined and innovated digital twins for years, how great is their true potential within the offshore industry? Multinational conglomerate Honeywell has been digital twins for several years now. We spoke to Honeywell general manager Manas Dutta to chart the future of digital twins.
Elliot Gardner: When we say ‘digital twin’, what does that mean within the oil & gas space?
Manas Dutta: So the term ‘digital twin’ has many different definitions depending on the industry, vendor or customer, but at a very basic level, a digital twin is a digital replica of a real plant. You can see everything about how the plant operates, which you can use to learn how to improve plant operations and its capacity utilisation.
There are many different ways to use that digital replica. Say you have a refinery or a petrochemical plant; you could use software to simulate the input and output chemical processes of that plant, experimenting with them without needing a physical plant setup. You could also replicate the physical look and feel of a plant. If a structure has, say, heat exchangers, distillation columns, compressor pumps, you can create a virtual replica of those aspects of the facility in virtual reality.
And you can also combine these two types of digital twin together, so you have a virtual replica of your physical plant that can be operated on in a virtual environment.
Elliot Gardner: What use cases are there for digital twins in the sector?
Manas Dutta: Let's say a new hire joins a plant. They can quickly learn about plant operations - say, how to do a start-up or a shut-down - in an integrated digital replica. We worked with a customer in North America building new LNG trains, but it was a greenfield project.
Typically once a plant is constructed, a new hire joins the plant and starts learning how to operate it. But the digital replica we created allowed them to train their people before the plant was even constructed, cutting down on months of waiting time.
Other use cases include developing ways to beat bottlenecking. If capacity realisation is not at its peak, you can experiment with different ways to change this through a digital twin without having to experiment on a live plant. Asset-related problems, like the performance of rotating equipment or compressor pumps, can also be looked at and improved digitally. So operational improvement, maintenance improvements, reliability improvements and training - these are all ways you can benefit.
Elliot Gardner: Oil and gas facilities can often be quite inhospitable environments - can a digital twin help cut down on physical visits?
Manas Dutta: Yes, that is definitely one very important use case. The more time a person spends in a petrochemical or oil and gas facility, the higher the chance of an incident.
A simple example is this: every two or three years a petrochemical plant has a shutdown for scheduled maintenance. There might be the removal of components, which would not be possible when the plant is up and running. To carry out this kind of turnaround, they have to plan properly. They might have to bring scaffolding into the plant, or even use a crane to move large components or equipment.
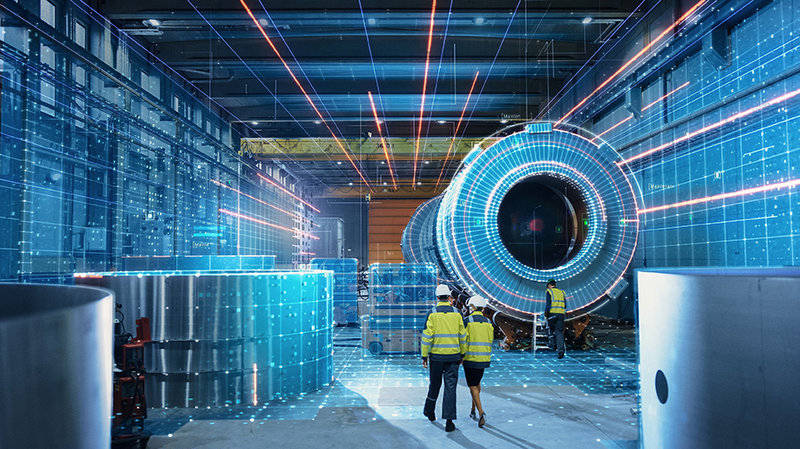
Digital twins replicate real facilities. Credit: Gorodenkoff via Shutterstock
Now, if you have a virtual replica of the plant, you can plan much more effectively. You can say ‘well, I have a 20-metre gap there so I can safely bring a crane in through here’, etcetera. All of that planning reduces the need for a person to physically inspect that space, reducing not only exposure, but the cost of those visits too.
Elliot Gardner: Virtual replicas have to be extremely accurate to be at all useful. How do you ensure the accuracy required?
Manas Dutta: It used to be difficult, but technology has evolved rapidly over the last few years. We now have very good laser scanning capabilities. Even if you don’t have a 3D model of a plant, a laser scan is accurate to between 5mm and 10mm.
And for the other side of digital twins, that’s when chemical processing software comes into the picture. There are two types of simulation that a digital twin undertakes when calculating these things: there’s the chemistry side of things, looking at how different components react to each other and different conditions, and the mechanical asset side, which analyses interactions between equipment like compressors or rotating equipment like pumps.
The way we are building digital twins is that there’s a machine learning algorithm built into it, which learns over time. So even if a digital twin isn’t 100% accurate to start with, it will continue to improve over time. We don't normally do anything unless accuracy starts from at least 80%, which is a good starting point for this kind of industry.
Elliot Gardner: Where do you expect the future of digital twins to go?
Manas Dutta: This space is really growing very fast. If we look at data analytics algorithms and machine learning within digital twins, artificial intelligence (AI) is sure to enter more into it. Digital twins today can provide some great predictive insights, but when AI is fully integrated within digital twins, they will be much more prescriptive, rather than merely being predictive.
Virtual reality is also evolving. We’re seeing more and more cost-efficient technologies that can be used to build a virtual replica coming into play. Eventually that will help not only with a simulated world, but will extend to augmented reality, which is not being used today specifically in the process industry. When we integrate augmented reality with digital twins, bringing that information in front of frontline worker operators and maintenance technicians, that will change the game.