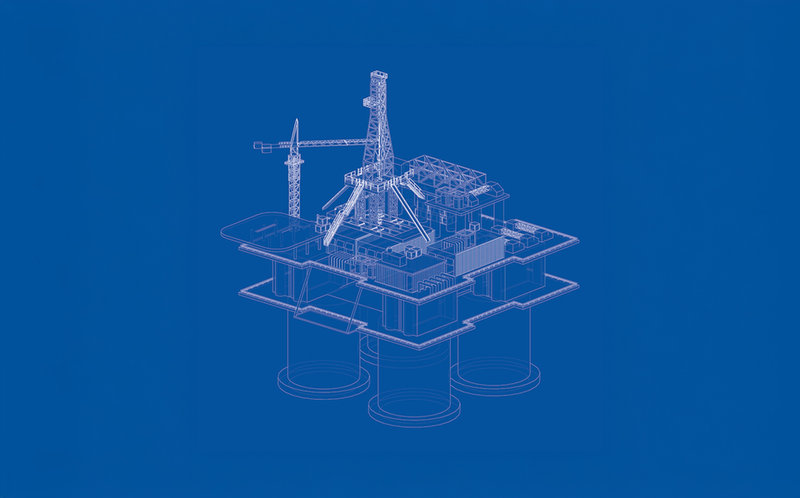
Companies have created twins of pipelines, gas plants, LNG terminals and refineries. Credit: Shutterstock
Digital twins are digital representations of physical assets, systems, people, or processes. These are rapidly becoming a mainstay in oil and gas operations as companies strive to optimise asset performance and minimise unplanned outages. This aims to make oil and gas operations relatively safer while lowering the carbon footprint and improving profitability.
Although the major emphasis is on creating digital twins for upstream projects, companies are also deploying these tools within their midstream and downstream assets for remote monitoring and predictive maintenance, among other benefits.
Digital twins can effectively simulate the management of oil and gas assets and forecast potential scenarios. Moreover, they can dynamically model the performance of an operating unit in real time.
The process of creating a digital twin begins with the construction of a comprehensive model. It is then coupled with inspection and sensor data coming directly from the asset. As fresh data is incorporated into the twin, the asset operator gains detailed insights into vulnerabilities within the asset. It allows them to implement maintenance and inspection procedures to avert downtime.
By harnessing real-time data, simulation, and analytics, digital twins can offer profound insights about operational assets. It can enable oil and gas companies to streamline processes, preempt breakdowns, bolster safety measures, and thus, enhance overall profitability. With their ability to provide a comprehensive view of operations, digital twins assist in formulating more informed and precise decisions, rendering them indispensable tools in oil and gas operations.
This technology was first deployed in capital-intensive oil and gas production facilities to streamline processes, mitigate emission footprint, and generate cost savings. Since then, companies have created twins of their pipeline systems, gas plants, LNG terminals, as well as refineries and petrochemical complexes. The eventual goal is to achieve autonomous operations at production units to boost safety and productivity.
Oil and gas companies are also keen on using this technology for their newer ventures beyond oil and gas, including in carbon capture and storage and renewable power projects. There is considerable potential for digital twins in these emission mitigation or clean energy projects. Besides facilitating remote monitoring, the technology can help companies to improve the efficiency and effectiveness of CCS projects and to predict the power output from wind or solar farms.
Another emerging use case for digital twins is in supply chain and inventory management, where products can be tracked in real-time to ensure their timely availability for end-use applications. This would help streamline logistics costs and maintain product quality for end consumers.
Further details of oil and gas companies and their adoption of digital twins can be found in GlobalData’s new theme report, Digital Twins in Oil and Gas.