Operations
Understanding offshore operations optimisation with ABB
With an unstable oil market, operators are seeking to optimise operations to make up for price fluctuations and increase cost-efficiencies. Alexander Love spoke to Espen Storkaas, ABB group vice-president for offshore oil and gas digital, at the company's Collaboration Operations Center in Oslo, Norway, to discuss how these relatively new technologies are transforming operations for the offshore industry and making automation a reality.
New technology, automation in particular, is rapidly changing the way in which industry operates across a wide variety of sectors. Although the offshore industry has at times been slow to adapt to technological innovation, digital solutions are now allowing operators to transform the way in which they manage work processes and improve upon operations. Although there is still work to be done with rolling out such solutions across the industry, technology such as that being deployed by ABB can add significant value to operations.
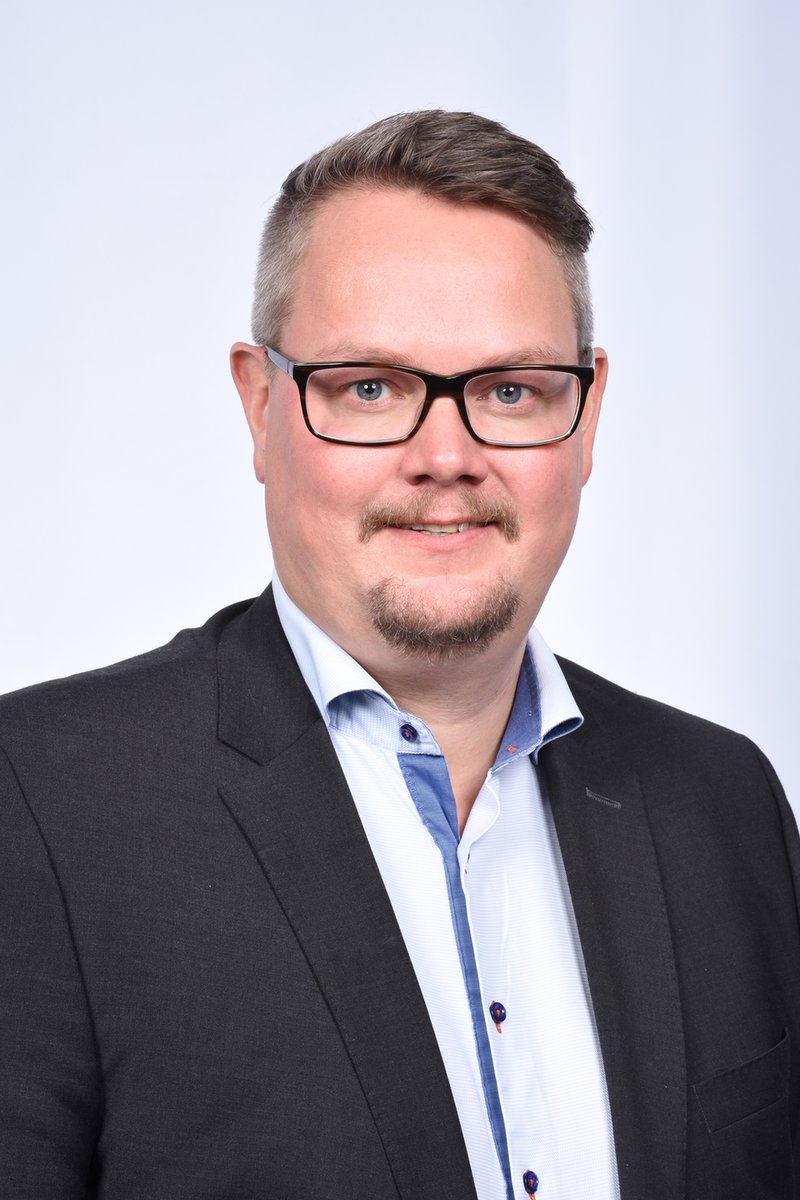
Dr Espen Storkaas
Alexander Love: What are the main advantages of using digital technology for oil and gas operations?
Espen Storkaas: I think it’s of great importance in the curve of continuous improvement. It is enabling things like significantly reduced maintenance. It reduces unuseful work processes. Take a switchgear: we took a look at that and said that we’re actually monitoring about 95% of the possible things that could go wrong with it. We’re still going out there and inspecting it while we still have the data. So, utilising data and changing our work processes, and stop doing what we shouldn’t be doing because we already have the knowledge. These are simple steps that can add significant value.
I think we’ll see an acceleration of this and a much more structured drive towards improvement.
How will this technology help oil and gas operators overcome many of the challenges they face?
One side of it is obviously being able to have a reduced cost base, which makes them more robust for volatility in the market prices. The other thing that in the extended services, it will allow you to operate with fewer manned rigs, with lower CO2 emissions per produced barrel. So, you will be able to have a lower carbon impact of production. So we’ll have that, as well as improved safety.
And at the end of the day, digital will be a significant contributor to having unmanned operations. Basically, it means autonomous assets sitting out there in the sea or in the vessel, operating by themselves. That is the end game.
How close is this technology to being rolled-out across the offshore industry?
There are many concepts that are on relatively simple plants. We have a lot of them already operating.
Our ability to remotely control and remotely monitoring what’s going on increases the complexity of what we can operate.
And then you have the extreme cases like subsea we are looking at now, which is the ultimate in unmanned. You’ll see a combination of subsea unmanned operations that optimised energy consumption to minimise emissions, which is predictable, remotely controlled and greener.
Can you give some examples of specific tasks where ABB’s digital technology can be deployed?
One of the good things about ABB Ability is that it’s a cross-industry platform, which means that we can access in a consistent manner technologies that are used in automation, that are used in the marine industry, that are used in pulp and paper, that are used in electrical chargers.
A turbine is a turbine, is a turbine, it’s a lot of the same technology. We’re now much more efficient because of digital tools to apply these from other industries to our industry and expand on that. So it gives a much more consistent set of tools and skill-sets.
Also, the networks that we’re building, there are centres like this for other industries that we can tap into. It’s now just a matter of collecting the data streams and the experts electronically. The ability to transfer learning is increasing significantly and so is the accessibility to expertise.
We’ve been working with a Shell plant up on the north-west coast of Norway, which is ten hours travel from here. If they need help from an ABB expert, they’re literally five minutes away. Not ten hours. He doesn’t have to occupy bed space, he doesn’t have to order flight tickets.
We can centralise collaborating operations. And with all our customers being able to subscribe into that model, we’re actually tapping into the collective knowledge of ABB, rather than the individuals we happen to have on-site for us. So it’s actually a game-changer in terms of our knowledge we have available to us.
How is this technology installed on assets? How is it connected?
It varies a lot. It ranges from monitoring to long-term optimisation, you just tap into a database and you extract the data. That can be done in batches, or it can be done by steaming just plugging into an API. With frontline monitoring, all sorts of devices are out there, where you’re actually pulling data from the device.
You come in with a little safe box, it just taps into, say, a variable speed drive or an instrument. It pulls the data out. It pulls the data out via a data diode, which means that data is only allowed to flow out from the device and not back into it – that’s physically prohibited, so it’s safe. It pulls it straight up to the Cloud.
Regarding software updates, is this done as a continuous process or in patches?
It’s a continuous process. We’ll see this delivered as a service, which means instead of deploying software at the facilities, software assigns here and the customer basically subscribes to the usage of it. That means that our developers are continuously monitoring things, they are looking for improvement areas. The operations guys will come in a say: ‘Hey, I’m tired of doing this manual process, can you automate that for me? How about we do this? How about we do that?’
So we’ll run this in a truly digital fashion, with lean processes, rapid prototyping.
The time from idea to actual implementation will get will much more compressed compared with what we had here in the past when we deployed the software, because then you had installation kit, it needs to be 100% foolproof, all those kind of things. You do this as a service and you actually have the subject matter, with experts and the developers sitting next them, so you can launch it much earlier because you have a safety net of the experts providing context and pulling out all the possibilities.
Do cyber threats influence the ongoing system development?
It’s certainly one of the key concerns that we have. Cybersecurity is a credibility thing. If you screw up a couple of times, you’re sidelined for quite a long time. So it is a licence to operate for people. It’s something we take extremely seriously.
It is perhaps the one part of the design process of new stuff that takes the longest time, because it is so critical. You can have the core technology ready in a couple of days or a couple of weeks, but you have to make sure that it is completely safe. That’s going to take you a long time.
So, it’s certainly the one we take by far the most seriously. And there is a huge apparatus in ABB that actually have to approve all the things we want to put online before we can do that. For someone like me, a market-driven guy, that can be frustrating, but it’s also quite a comfort to know that there are various people checking that that this is absolutely safe.
You’ve been with ABB since 2005. What would you say are some of the biggest changes to the upstream oil and gas industry in the time that you’ve been working for the company?
The biggest changes have happened over the last three or four years since the oil price dropped. Because if you looked at the boardroom priorities up until maybe 2013, they talked about reserve replacement, it was people looking for oil to make sure they had a backlog of produced oil. That was really the only thing driving the business and that was how companies were evaluated. Now the stock prices of the oil companies is much more driven by cash-flow
They’re now working on much tighter margins than they did in the past. Even though nowadays again their cash-flow starts to look good, productivity has taken centre stage.
This is really some of the things I’ve been working on for a number of years, trying to find advanced control solutions to get more out of wells. It’s a lot easier to talk about that when the oil price is $55 a barrel than when it’s $115. So I think the drive towards improvements on the operations basis is perhaps the biggest change and that’s happened over the three or four last years. Before that, it was boom times, projects all the time and basically putting enough people on the job. Now it’s a different story.
In some ways, this is more fun because it’s opened up more creativity to find good solutions.
And then you’ve got new dimensions coming in. We’re looking at new concepts with mixes of renewables and oil. We have to think of new things now, because the demands are higher.
We’re moving into a more interesting time for the industry. It’s more fun because it requires more creativity and ingenuity to find good solutions. I don’t buy into the doom of the industry quite yet. I think we’re moving into an interesting period.