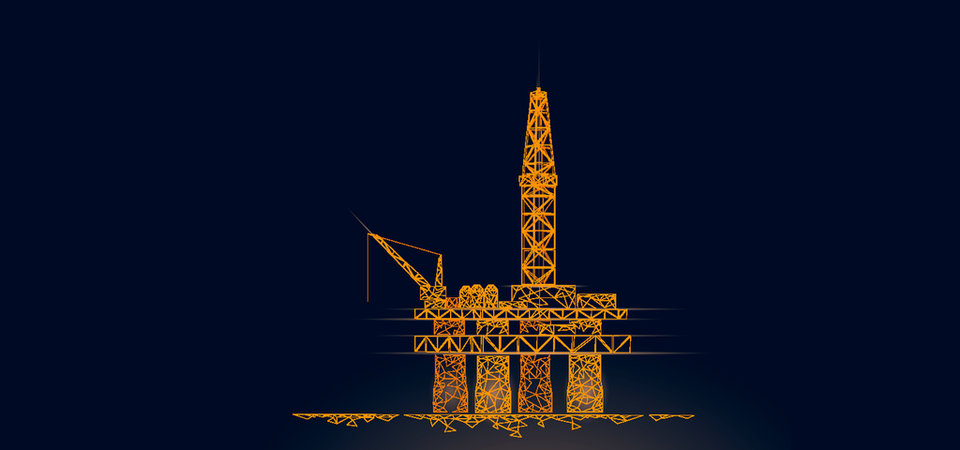
TECHNOLOGY
Testing digital twins: do they work in oil and gas?
Digital twins are a hot topic in a few industries, but what’s the true operational value of creating digital copies of complex infrastructure such as oil and gas platforms? Yoana Cholteeva looks into the challenges in implementing digital twins, and the importance of smart integration to get the most out of this technology throughout an asset’s lifecycle.
B
y adding predictability, time and cost savings, and product quality, digital twins have established an important role as part of the manufacturing industry, and they are now starting to prove their worth across the oil and gas scene.
According to IBM, digital twins arrived just in time as a new set of manufacturing and construction tools were needed to meet the new realities of software-driven products.
“Thankfully, the advent of digital twins offers engineers a technological leap ‘through the looking glass’ into the very heart of their physical assets. Digital twins give us a glimpse into what is happening, or what can happen, with physical assets now and far into the future,” IBM said in the article ‘Cheat sheet: What is Digital Twin?’.
While digital twin technologies are still adjusting to the challenging conditions that oil and gas platforms often operate in, experts across the industry are eagerly anticipating great success.
Developing digital twins in oil and gas
There is an opportunity for digital twins to make a mark in the energy sector, by featuring a mixture of different solutions that, for now, offer one dimension of information about part of the lifecycle of an offshore asset, such as 3D and 4D design.
Chief technology officer at Wood, a global leader in engineering and consultancy across energy and the built environment, and author of ‘The rise of digital twins: Delivering on their promise’, Darren Martin says: “This technology is using real-time data to be able, just by a click of a button, to draft major asset designs.
In many cases, the oil and gas industry is using limited and antiquated design concepts
“However, in many cases, the oil and gas industry is using limited and antiquated design concepts, relying on feedback loops slowing down the process – It’s time to embrace digital twin technology and understand which aspects are applicable to the industry.
“Once an asset is put into operation, the intelligence about how to make it perform better is really disaggregated. So, the opportunity is to bring expertise around how to design an asset with the right digital information and right capabilities at a pre-feed and feed level, so that the intelligence is designed into the asset from the beginning.”
In this regard, Martin points out that a number of companies are still on a journey where they understand how to integrate some of the data and provide some of the services, but they don't necessarily know how to adapt and learn from that information to derive more value.
Competing design ideologies
Currently, there are competing ideologies and approaches on how to design an asset that can be run at lower costs but with high productivity, which makes it hard to navigate the scene.
Some of our clients have spent a lot of money with original equipment manufacturers and software providers
“Some of our clients have spent a lot of money with original equipment manufacturers and software providers so they already have good technology in operations, but it’s often disconnected. So, the opportunity for our client operators is to look at their preferred partner choices, and then working with them to unravel challenges, by applying a consistent technology ecosystem across the full asset lifecycle,” Martin says.
This concept seems to be relevant from an offshore perspective across oil rigs, along with wind turbines and hydrogen technologies, but no matter the asset, Martin explains that “it's really important to figure out what's been done so far, what's left to do, what can we learn from doing that on a particular asset and what does that mean for an operator at scale, what does it mean for them across the region, and what does it mean for them globally”.
Saving costs and making the most out of asset lifecycle
Digital twins can usually be incorporated to help in three various scenarios – designing a new asset, working with an existing asset going through a major upgrade, and optimising an existing asset.
Martin shares: “We are working in a partnership with BP to create digital twins of their North Sea assets, linking this to key documentation, data, and the plan of work. This allows the planning of work to be completed onshore from anywhere in the world.
“This, coupled with analytics means that the teams can act on opportunities to complete the right work and maximise site productivity. For those carrying out modifications, they gain easy access to key documentation and laser scan models of the assets. This speeds up the design process and reduces persons on board and cost.”
Our partnership with BP focuses on using innovation to create value
The digital twins allow work once done offshore to be moved onshore, eliminating the need to mobilise offshore to see and inspect the asset, providing powerful insights into the plan of work that can be used by the teams to maximise productivity. This reduces the number of personnel mobilising offshore, resulting in lower emissions and the cost of executing work.
“Our partnership with BP focuses on using innovation to create value by transforming the way we approach, plan, and prepare work. The partnership is a joint investment and outcome based on where the value created is shared,” Martin says.
Trying and testing digital twins
As digital twins are treated as complementary to an automation control capability, many safety critical processes are dealt with on the supervisory control and data acquisition and distributed control systems, which control the critical process that effectively stops hazardous activities from happening.
Martin explains: “As we don't want to have a fire or a leak on an offshore asset, a lot of the information that's still within that control room capability is traditionally dealt with very close to the asset, and there are operators that are ready to look at the information and shut tasks down so that there isn't a fatal risk to life or the environment. We are also seeing more and more opportunity to centralise control capabilities onshore.”
We are also seeing more and more opportunity to centralise control capabilities onshore
The digital twin will warn that there's a real problem with an asset and depending on how accurate this information is, the company will send operators to fix remote assets. But what if there really isn't anything wrong?
Martin elaborates: “How do we evolve users’ thinking from, ‘well my car alarm keeps going off. I don't trust my car alarm’? So, when it goes off and someone is actually robbing my car, I'm not going to listen to it because it keeps going off, because it's temperamental.”
A successful ecosystem for digital twins
These risks make it extremely important for the technology providers to use their information and help operators understand it to reinforce trust instead of undermine it.
This enables digital twins to provide “a bedding in period between always doing tasks manually to trusting the system. And sometimes the data that the system provides will be incorrect and there's a refining process, so it becomes more and more trusted”, Martin explains.
Looking into the current problems that digital twins come with, it appears that they are more associated with approach, rather than technology, with issues of traditional financing and over-dependence on single suppliers standing in the way of improvement.
Above all, successful digital twins are about a successfully-led ecosystem
Reinforcing this idea, Martin says: “Above all, successful digital twins are about a successfully-led ecosystem; no single company can do all this alone. Instead, strength comes from networks and a real alliance. That is how science fiction becomes a digital fact.”
Talking about alliance, as one of the latest company ventures, Wood has joined forces with US software provider AspenTech to hopefully develop autonomous plants of the future.
“And that's all about taking that information about how our assets are performing, interpreting it and ignoring the anomalies until the information is more and more trusted. Then our operators start to harness this technology, say in Africa, in the Middle East, and in Asia, helping to make the concept of autonomous capability more realistic. So that's where we are at,” Martin concludes.