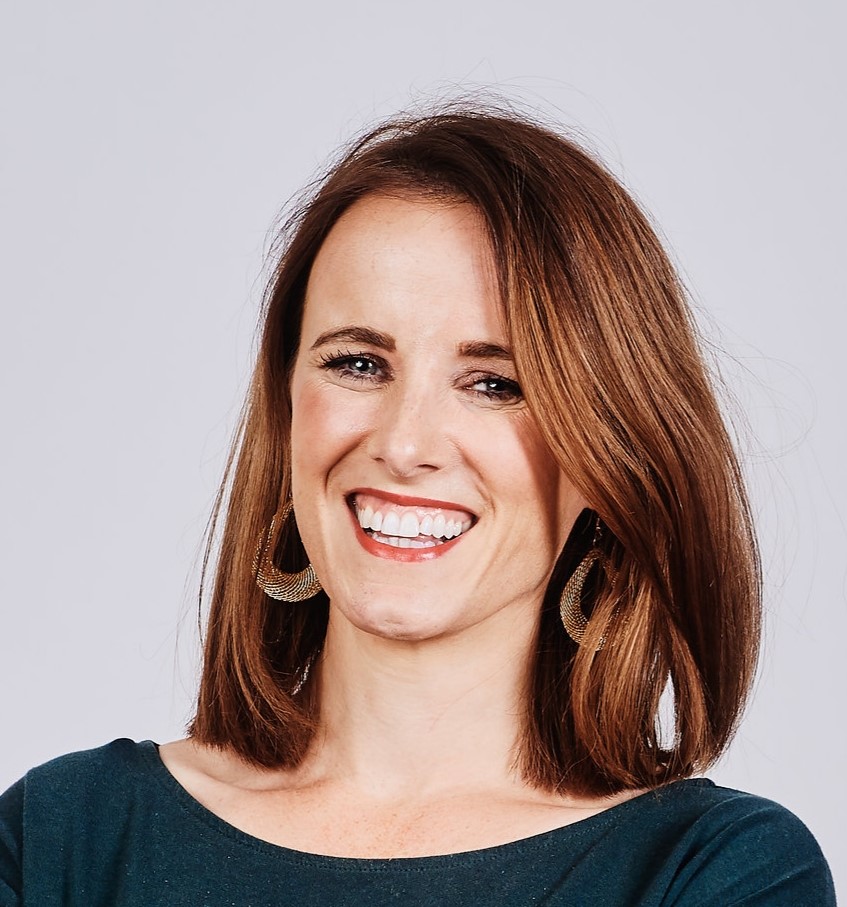
Amy McCleney, research engineer at Southwest Research Institute. Image: Southwest Research Institute
Q&A | SAFETY
Talking blowout prevention with SwRI’s Amy McCLeney
With the tenth anniversary of the Deepwater Horizon disaster approaching, Umar Ali speaks to Southwest Research Institute research engineer Amy McCleney about the latest innovations helping to improve well safety and preventing blowouts.
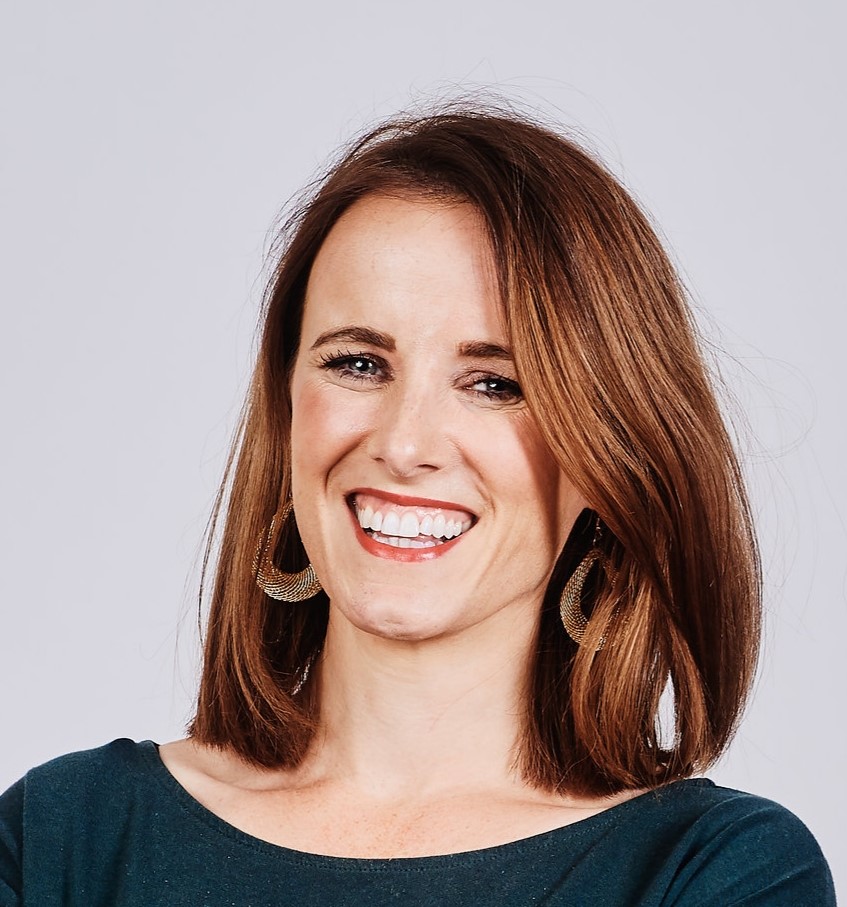
Amy McCleney, research engineer at Southwest Research Institute.
Image courtesy: Southwest Research Institute
Credit: Courtesy of Cognite
T
he Department for International Trade (DIT) is responsible for promoting international investments and trade in the UK, as well as developing trade policy framework. As new markets are developed and the financial landscape is shifted by changes like Brexit, the DIT works to ensure investments in the UK remain stable and profitable.
In the thick of it is Campbell Keir, Deputy Director of Energy and Infrastructure responsible for the Oil and Gas, Renewable Energy, Civil Nuclear and Infrastructure portfolio.
The Deepwater Horizon oil spill is probably one of the most public crises the oil and gas industry has faced in recent memory, with 11 dead, 17 injured, and 4.9 million barrels worth of oil spilling. Now, as we approach the tenth anniversary of what is considered to be one of the worst environmental disasters in American history, it is worth exploring how far along the industry has come in developing technology to prevent and limit similar disasters in the future.
In order to find out more, we spoke to the Southwest Research Institute (SwRI), an independent, non-profit, applied research and development organisation about their work around well safety and how they see similar work being applied across the industry.
Umar Ali: Could you give a brief overview of the ANSYS simulation technology that SwRI has been testing?
Amy McCleney: Overall, the intent of this project was to find a way to adequately assess blowout preventers and specifically blind shear rams.
In the past, with this type of assessment, most manufacturers of blind sheer rams only look at mechanical properties such as diameter and thickness, but when a blowout preventer is used in those scenarios, you have fluid flowing through it.
In terms of assessing blind shear rams through a testing programme, there's not a facility in the world that can do this right now. So the idea behind this project was to develop this computational approach to assess blind shear rams under operating conditions.
And we wanted to use a commercial software so that in the future, these manufacturers also do this assessment on their end. So we needed to figure out what simulation approach we needed, to take a commercial software so that the end user could eventually use the software to do the evaluation on their own.
How the simulation technology works is we do a finite element analysis in one software. Basically, we simulate the blind shear ram shearing the pipe - pinching it off and cutting it. Then we take the information that we get from that computational analysis and we feed it into a fluid analysis, so the idea is that both software are talking back and forth to each other.
We’re able to get information such as “Are there any fluid forces that are pushing back from the rams that are preventing it from closing? Is there something weird that's mechanically happening with the blowout preventer in the simulation that would prevent it from closing?”
We’re nearing the ten-year anniversary of the Deepwater Horizon disaster. How has safety technology progressed in those ten years?
In terms of responses to the Deepwater Horizon disaster, here in the US we have the Department of the Interior and we have a brand under the Department of the Interior called the Bureau of Safety and Environmental Enforcement.
Their goal is to ensure that our technology, including blowout preventers, is continuously being improved, and they’re the ones who enforce the regulations. Their brand is dedicated, since the Deepwater Horizon incident, to improving these technologies and making sure we're being innovative and safe with our research.
Since the Deepwater Horizon incident led to the founding of this regulatory body, I believe that the technology for blowout and oil spill prevention has improved significantly since then.
What more do you think needs to be done in order to improve safety technology going forward?
For our work with blind shear rams and blowout preventers, we only look at a small portion of the simulation approach. Basically, our job was to figure out how to do it, we didn't test or consider a wide range of scenarios, which would help manufacturers make more informed decisions about their safety systems.
There's an entire suite of conditions that we didn't have time to look at. It’s kind of like an onion, right? We got the outer layer, we peeled it away, and we're still kind of peeling away at that onion.
We found the best simulation approach, but we need to find how to use it under different scenarios and different conditions to actually help regulators and manufacturers design a system that is the most safe for the intended environment.
What do you think are the most exciting innovations in safety technology?
It's hard to say because the oil and gas industry tends to not want to reinvent the wheel if something works. So there hasn't been a whole lot of innovation in the last few years that I've been involved in the oil and gas industry, but it's basically been taking what's already existing and tweaking it in a way so that's it slightly improved.
If something breaks in this field, you're not only talking about safety concerns, but also loss of revenue, loss of down time, and cost to repair. Simulation technology is helping with this - the cost-benefit of this simulation approach is if eventually there is some sort of new innovative product that comes out, companies can do more of a design space exploration.
If we've already figured out the approach to simulate new blind shear rams or blowout preventers we can take these new designs and then slowly iterate their geometries to see how they will perform in the field before they're mass-produced. This is useful for helping improve safety, and also useful for the manufacturers of these devices- it saves money and resources for the whole iterative prototype design process, which can be very costly.
If you could tell the oil and gas industry one thing about improving safety, what would you say?
I guess I would tell them to be more proactive about trying to figure out what is going to be the worst-case operating scenario that my equipment could be exposed to.
A lot of times, even with our testing programmes that we have here at SwRI, we get equipment that says it's within this operating range or within certain pressure or pulling conditions.
But if on the well you experience something like a formation kick in a blowout, they don't actually know how that piece of equipment is going to respond. So my response would be “be more proactive about these extreme cases.” Even if they are extreme situations, what would your response be if the worst-case scenario actually happened?