TECHNOLOGY
Innovations in plug
and abandonment
With decommissioning being an increasingly important field for oil and gas operators, companies have invested significantly in technologies that could reduce the time and cost of these essential operations. Umar Ali explores the new systems that could improve the plug and abandonment process.
Credit: Henning Flusund
With decommissioning perhaps more on the industry’s mind than before, finding new ways to innovate in this area and ensure that the plug and abandonment process is going ahead as safely and smoothly as possible is becoming ever more important. With this in mind, several companies are developing new technologies and systems that could improve upon current techniques and allow companies working in the offshore sector to cut the cost and time requirements of traditional plug and abandonment processes. Below, we explore some of the companies innovating in this area and the solutions they are bringing to market.
Deep Casing Tools: Casing Cement Breaker
Aberdeen-based oil and gas technology development company Deep Casing Tools is preparing to bring its Casing Cement Breaker tool to market, following a successful trial with Norwegian energy multinational Equinor in May 2019.
The Casing Cement Breaker is currently being developed in collaboration with Equinor, French oil and gas multinational Total, and the Oil and Gas Technology Centre (OGTC).
The tool uses pressure and rotation to manipulate existing casing strings, breaking the bond between well cement and casing in plug and abandonment operations.
This reduces the time and cost of decommissioning operations compared to traditional abandonment methods including perforate and wash, cut and pull, and milling, by simplifying and streamlining the abandonment process, even removing the needs for methods such as milling entirely.
Deep Casing Tools CEO described the technology: “We’ve proven it breaks down the bond between the cement and the casing, as well as the structure of the cement behind the casing, and that it reduces the forces needed to remove casing – by around 50% on this first trial.
“We expect to achieve 90% reduction as seen on testing with future generations of the tool. For operators, this means less time and cost. You can pull longer sections with less force, fewer trips, fewer cuts and less rig time.”
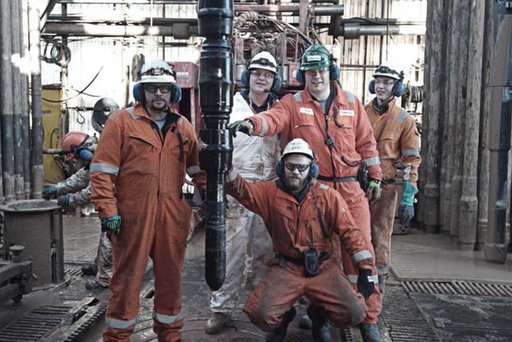
Image: Deep Casing Tools
Interwell: Rigless plug and abandonment
Norwegian company Interwell has been developing a rigless approach to plug and abandonment since 2012, and has run trials in 18 different wells across the world since 2016.
The technology uses wireline cabling as a deployment method to create “formation-to-formation” barriers across multiple strings of pipe.
A tool system is positioned in the cap rock region, followed by a barrier tool which is activated by an electric signal. This activation initiates a slow-burning exothermic reaction at high temperatures, which causes the reactants to melt through the surrounding materials and bond with the cap rock formation.
This process, which is similar to naturally-occurring magmatic processes, restores the cap rock formation to its original integrity and results in a solid barrier that extends across the full cross-section of the well and seals horizontally as well as vertically.
According to the company, this method could be a cheap and quick alternative to traditional cement plugs. The method also removes the need for section milling and casing removals, time- and energy-intensive parts of traditional plug and abandonment.
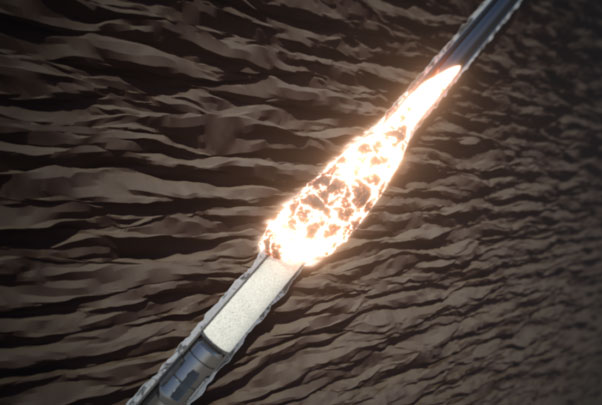
Image: Interwell
Clearwell Technology: Therm-X-Mill
UK-based company Clearwell Technology is developing the Therm-X-Mill high-energy thermal device for downhole, in-situ removal of production tubing components.
Similarly to Interwell’s rig-less system, Therm-X-Mill works by using a “modified high energy process” to produce a high-intensity jet that melts through sections of well bore tubing string, enabling the installation of an effective barrier. This eliminates the time and resources required to recover completion string out of a well during plug and abandonment.
Clearwell’s research has been supported and funded by the Oil and Gas Innovation Centre (OGIC) in collaboration with the OGTC, with the research itself being undertaken by the University of Strathclyde’s chemical engineering team.
Clearwell CEO Paul Ray said: “As we progress along the journey to commercialising Therm-X-Mill, we are going through new territory, it is exciting, but also unfamiliar.
It’s been invaluable to have the financial support and practical guidance of OGIC and the technical input of the academic team at Strathclyde University along the way.”
BiSN: Wel-lok M2M
UK-based downhole sealing solutions company BiSN, in conjunction with Atlus Intervention and Norwegian oil and gas company Aker BP, deployed its Wel-lok M2M well plug in the Norwegian North Sea in October 2018.
Wel-lok M2M is designed to bring substantial savings to operators decommissioning wells, and is currently the largest well plug made from bismuth. The technology uses a modified thermite chemical reaction heater to melt bismuth-based alloys downhole.
While technologies such as Interwell’s system and Therm-X-Mill use similar downhole technologies in plug and abandonment, BiSN’s plug and abandonment solution stands out through the bismuth alloys, which have a viscosity similar to water and a specific gravity ten times higher than that of water.
The unique qualities of these alloys allow them to flow into smaller areas of wellbores, creating an airtight seal without the need for surface pumping equipment, saving the time and resources needed to operate this equipment.
Much like similar innovative technologies Wel-lok M2M eliminates the need for milling, and can even be used in corroded or damaged well casing.
Describing the initial trial in Norway, BiSN CEO Paul Carragher said: “This project is an important step towards the adoption of bismuth well sealant technology. Wel-lok M2M drastically reduces the rig time needed to complete well abandonments through the use of thermite heaters to melt bismuth-based alloys.
“We are fundamentally changing the way downhole sealing is carried out, and through trials like this, we continue to break the mould of traditional methods, changing the way operators look at well abandonment.”
Video: BiSN