Comment
How new technologies can change fire safety
In a petrochemical-rich environment, fire safety is the first concern. Nnamdi Anyadike takes a look at recently-launched fire safety devices.
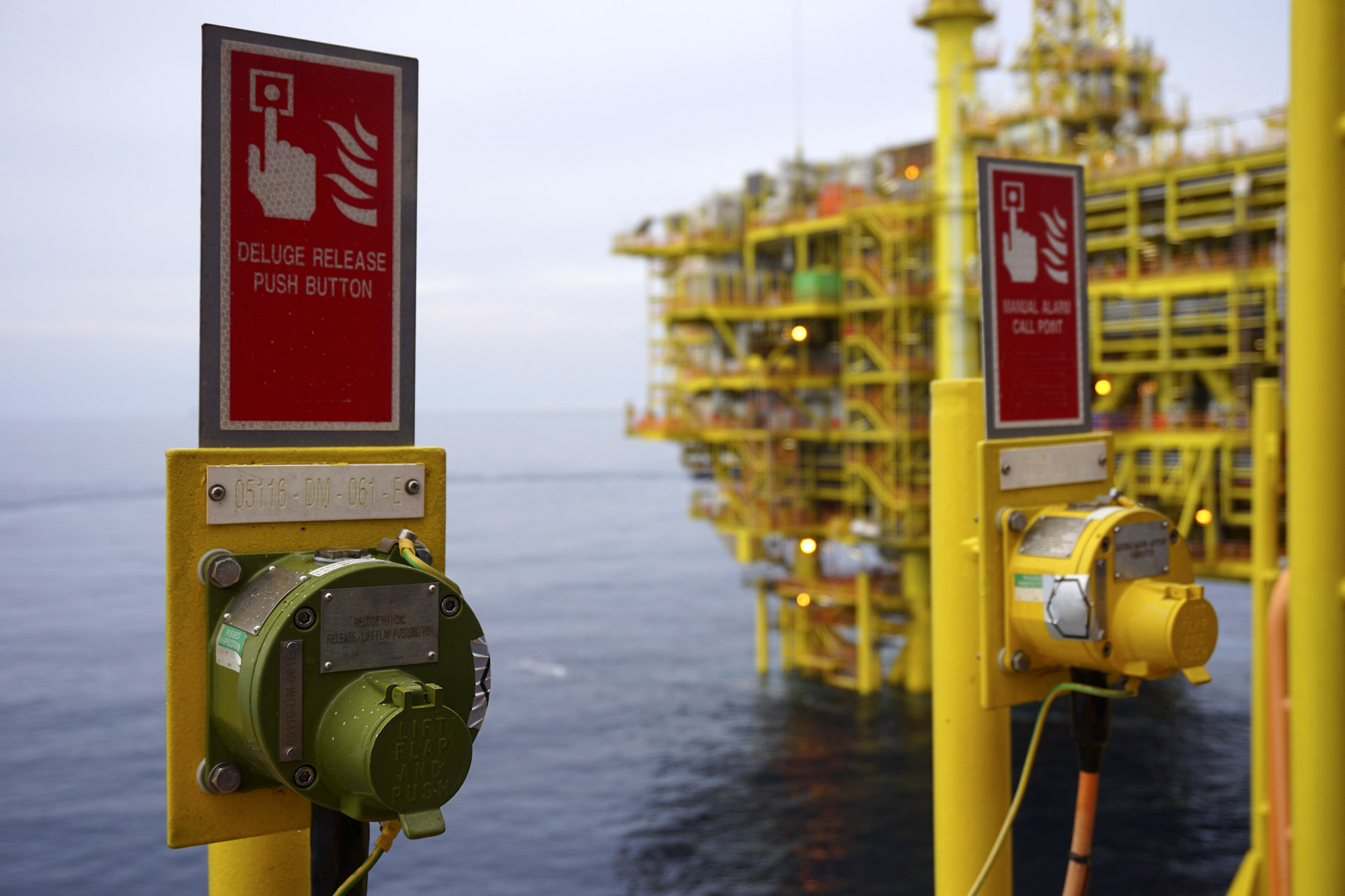
Fire safety is never far away. Credit: Opsorman / Shutterstock
Much is made of how the advance of technology will increase productivity and optimise processes, but this rising tide can also improve more important technologies. Fire is a constant risk in oil and gas extraction, and despite generally widespread use of current-generation technologies, incidents continue to occur.
Drilling rigs, oil tankers, floating production storage and offloading (FPSO) vessels, offshore support vessels (OSVs) and other related equipment all require fire safety equipment that minimises risk and does not itself pose a risk of sparking or overheating. Aside from the obvious risk of loss of life, at minimum, fire events cause a loss of work time and reputation, sometimes on an international scale.
In February 2022, an explosion on the FPSO vessel Trinity Spirit, off Nigeria, killed at least three and engulfed the facility in flames. Over the next few months, Altera Infrastructure’s FPSO vessel Petrojarl Foinaven and Equinor’s FPSO vessel Johan Castberg both caught fire, causing the evacuation of crew in each case.
Of 118 workers, 65 were evacuated from Equinor’s Aasgard B oil and gas platform, following a fire in a transformer last November. Then in December, Shell’s Prelude floating liquefied natural gas (FLNG) facility offshore Australia caught fire. This followed an earlier fire the previous December that caused the facility to be closed until April 2022.
Last June, three platforms operated by the Crimea-based oil and gas company Chernomorneftegaz caught fire, injuring at least three. However, this may represent an entirely different risk, as the Russian military alleged that this came as a result of attacks by Ukrainian forces. Similarly, some publications mused on the possibility of intentional sabotage by partisans supporting Ukraine when a fire injured at least seven in December. Despite its ferocity, owner Irkutsk Oil Co did not comment on the fire at the Markovskoye field, an oil and gas condensate field in the Irkutsk region of Siberia, Russia.
Fire protection, detection, and prevention systems combined
Fire protection systems used in oil and gas process facilities typically fall under four categories: water and foam fire suppression systems, fire extinguishers, fire alarms, and fire safety training. These systems can be costly, requiring continual maintenance and worker training. But at their heart, they all seek to minimise loss to field operators.
Vanguard Fire & Security Systems, a US based provider of oil and gas fire protection solutions, says the biggest risks occur when oil escapes from its containment where a stray spark can ignite and start a dangerous fire. Common petrochemical fire and explosion hazards include boiling liquid expanding vapour explosion (BLEVE), explosions, flammable liquid pool fires, flash fires, jet fires, and more usual combustible fires.
Establishing an emergency response plan is only the first step
Gavin John Lockyer, CEO of Arafura Resources
Vanguard says an Emergency Response Plan (ERP) is crucial for oil and gas facilities to combat fires, but establishing an ERP is only the first step. The plan needs to be constantly reviewed, and every employee and operator in the facility needs to be thoroughly briefed and kept up to date on the procedures. It is also important to evaluate available resources based on the worst-case scenarios outlined in the plan. Equipment also needs to be constantly evaluated, and training undertaken to a high level of realism.
As Vanguard points out: “It’s one thing to have an emergency response plan. It’s another to ensure the plan actually works in a real-life situation.”

Mines in Bayan Obo in Inner Mongolia, China, extract one the largest deposits of rare earth metals found in the world. Credit: Bert van Dijk/Getty images
New fire protection systems unveiled
Over the past few months a number of companies unveiled fire protection systems for oil and gas assets. In April, Norwegian chemicals company Jotun launched its Jotachar JF750 XT, an all-climate coating for petrochemical infrastructure. The company describes it as a “two-component, solvent-free, amine-cured, 100% solids epoxy intumescent coating,” developed using the company’s unique, patent-pending technology.
The Jotachar JF750 XT features low installed thickness and self-reinforced flexible binder technology. It is designed to protect critical steel structures against combined cryogenic spill, hydrocarbon and jet fire scenarios.
In the US, Pennsylvania-based manufacturer of gas and flame detection systems MSA Safety Inc recently launched its new HazardWatch FX-12 fire and gas system, with built-in cloud-ready capabilities. The company claims the system, “represents the next generation in highly-intelligent monitoring solutions designed to help customers reduce hazard vulnerability.” The system was developed with industrial automation specialists Rockwell Automation.
The company claims the system can cover all aspects of oil and gas production, from production to tanker loading and unloading, as well as petrochemical refining and storage, pipelines, gas compressor stations and LNG facilities. The technology provides a stand-alone local fire and gas alarm panel, a redundant power supply to support the fire and gas system, easy integration with third party auxiliary devices and fire suppression systems, and FM-approved EtherNet/IP system communications.
Using GPS and IoT devices in fire detection systems
Last year, San Francisco-based Advanced Technology Products (ATP) trialled a GPS-based proof of concept in Australia. The fire and gas detection specialist conducted its internet of things-based (IoT-based) trial at the Karratha integrated LNG, domestic gas, condensate and LPG facility located about 1260 kilometres north of Perth, Australia.
The Karratha gas facility operator sought to capture improved data on the location of vehicles, equipment and personnel on-site, and to investigate enhancements in emergency fire response in and around the operational facility. “The project used GPS-based tags instead of just Wi-Fi tracking; one of the first deployments using the tags,” an ATP statement said.
This was the first solution designed and implemented on a live gas plant
The company also worked on a ”hazard-proof data system” at the Ichthys LNG radio-frequency identification (RFID) project in Perth, Australia.. The operators of the facility, one of the largest LNG projects in the world, aimed to mitigate hazard concerns, including gas leaks, explosions, cyclones, electrical faults and high-pressure environments.
The ATP system provided an active RFID system operating on a wireless network. This is the first such solution designed and implemented on a live gas plant for enhanced monitoring and safety. The company also developed a fire monitoring solution for Thailand’s PTT Global Chemical (PTTGC), the country’s largest petrochemical and refining company. An ATP statement describes the system as “an explosion-proof fire monitoring system, that can be controlled both locally and remotely to provide the client with better visibility of potential obstructions”.
Technology and automation expands the fire suppression systems market
The global fire suppression systems strategic market is rapidly growing, with one report suggesting that it will rise from $19.7bn in 2022 to $28.8bn by 2030. The dry chemical-based fire suppression segment alone is projected to record a 5.4% compound annual growth rate, and reach US$11.8bn by the 2030. The rise of “smart technologies”, robotics and automation acts as a key market driver behind this, Making fire protection more effective and safer for staff. Alongside IoT systems, advanced sensor and detection systems, rich user interfaces and intelligent software, these systems hope to create a new approach to fire prevention, hopefully enhancing worker safety in future.