Feature
Assessing the biggest refinery technology changes by 2030
Over the next five years, advanced refineries are set to make giant strides in energy efficiency and digitisation. By Claire Jenns.
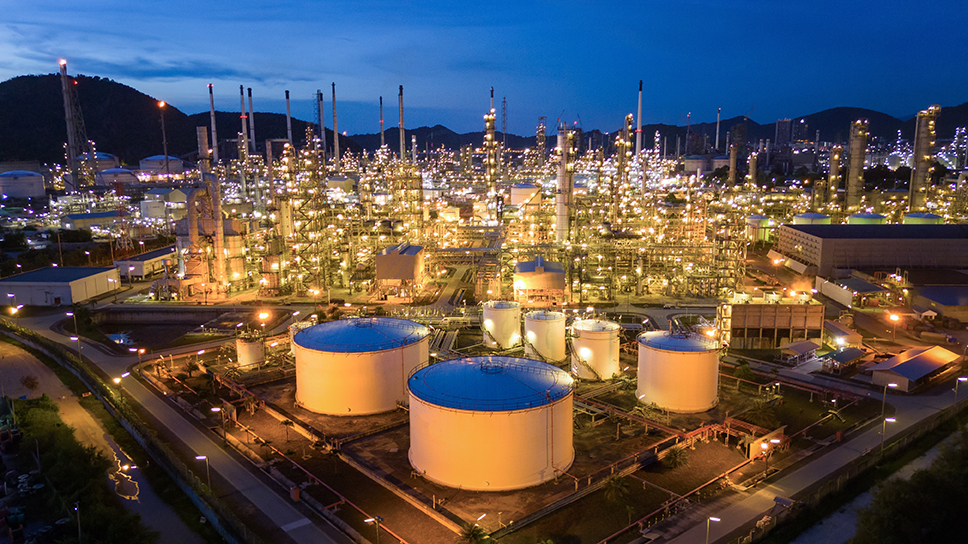
Credit: GreenOak / Shutterstock
As energy security and the optimisation of hydrocarbons have become global priorities, the role of refineries – a key element in turning an extracted substance into something valuable – has grown in importance.
Refining crude oil supports the manufacturing of over 6,000 everyday products and high-tech devices across a range of sectors, including the pharmaceutical, transportation and electricity generation industries spread across the globe.
To meet this demand, Offshore Technology’s parent company GlobalData forecasts that global conventional refining capacity is expected to increase to 12.9 million barrels per day (mbbl/d) in 2028 at an average annual growth rate of 3.4%.
This increase in capacity, led by widespread reliance on petroproducts, requires refineries to boost efficiency while simultaneously balancing reduced emissions and energy usage in line with global energy transition goals.
Speaking to Offshore Technology, Dr. Alexander Krajete, CEO of emissions specialist Krajete confirms that “reaching sustainability targets in refining is growing more challenging, but it’s far from impossible.”
Indeed, technology investments in the refinery sector have enabled the integration of renewable feedstocks, advanced distillation processes and digitised operations led by artificial intelligence (AI) to mould the refinery of the future.
Co-processing feedstocks
As the first step in the refining process, using a variety of raw materials as feedstock offers broad potential for technical innovation.
Co-processing enables refiners to combine petroleum and bio-based feedstocks to produce fuels with lower carbon intensity. Existing units can be converted for co-processing or standalone refineries can be purpose-built.
The primary feedstock for refineries is crude oil, useful for its complex mix of chemical compounds that produce high energy density products such as gasoline, diesel and lubricants. However, the sulphur content of crude oil is highly polluting, increasing the risk of variations in product quality and the corrosion of operational equipment.
Consequently, the industry is integrating alternative feedstocks for refinery optimisation and diversification. The International Energy Agency (IEA) highlights the shift towards petrochemical feedstocks which allows hydrocarbon companies to “pivot production as market conditions warrant.”
Shortage of feedstock may lead to unfavourable practices, such as deforestation.
Gavin John Lockyer, CEO of Arafura Resources
Petrochemical feedstocks include liquid petroleum gas, ethane and naphtha which produce sought-after plastic and chemical products, increasing the value of refining streams. As with crude oil however, the environmental costs are high, with petrochemicals comprising 6.1% of global emissions by end use from carbon trapped inside the products.
Renewable feedstocks have become increasingly popular to help decarbonise refinery processes. Biomass such as vegetable oils, animal fats and agricultural waste can be co-processed with traditional fossil feedstocks through hydrotreatment technology, which uses hydrogen at an elevated temperature to remove impurities. This produces biofuels which are predominantly used in the transport sector.
The potential of renewable feedstock technology has been endorsed by investments from industry giants. To reach its biofuels target of 50,000 barrels per day globally in 2025, BP has invested over $250m in coprocessing at Cherry Point, the largest refinery in the Pacific Northwest.
While the use of renewable feedstocks can significantly reduce carbon intensity and emissions, GlobalData’s ‘Circular Economy in Oil and Gas’ report points out that “the probable downside is availability in sufficient volumes to meet the market demand. Shortage of feedstock may lead to unfavourable practices, such as deforestation.”
The volatility of the downstream oil and gas supply chain, which is vulnerable to climate change events and geopolitical conflict, means that co-processing a range of feedstocks enables refiners to adapt to material shortages and new product markets.
Investments in traditional, petrochemical and renewable feedstocks and co-processing technology will be a mainstay of refining by 2030, not least to meet the forecasted peak demand for oil and gas.
Developing distillation processes
Similarly to feedstocks, refiners are exploring alternatives to traditional distillation technology which has an estimated average energy consumption of 30-40% in refining operations.
In 2026, GlobalData predicts the year-on-year growth in global distillation unit capacity to reach 117,424 thousand barrels per day (bpd), driven primarily by new builds and advances in technology.
The most common method used is fractional distillation, which separates crude oil into different petroleum components within a column based on their boiling points. The heat and water-intensive process requires significant energy, pushing the hydrocarbon industry to explore alternative methods for lowered emissions.
Atmospheric and vacuum distillation have become increasingly prevalent in refineries, allowing for the complementary separation of substances at normal and low boiling points. Vacuum distillation is useful for commodifying residual hydrocarbon waste streams to make products such as asphalt and bunker fuel for marine vessels and industrial boilers. However, these distillation methods can cause high levels of corrosion due to steam condensation.
A breakthrough in distillation technology has emerged, researched by ExxonMobil, Imperial College London and the Georgia Institute of Technology (GIT). Synthetic membranes have been used to separate complex hydrocarbon mixtures through the application of pressure instead of heat.
Professor Ryan Lively from GIT tells Offshore Technology that this process “is significantly more energy and carbon efficient than distilling oil and similar chemical mixtures. The membrane system can reduce the energy of initial distillation columns by about a factor of two now, and that’s just our first try. A factor of two on 1% of global energy usage is quite a lot.”
Membranes remain under active development for commercialisation. Lively confirms that membrane technology was successfully deployed in the US oil and gas industry in the 1990s for the separation of lubricants before falling out of use.
“Now the challenge is we have to re-convince oil and gas and membrane manufacturers to engage in this journey again,” says Lively. “The prize is big in terms of energy and emissions reduction, so I feel confident someone is going to run with it.”
Enabling AI and data-led refineries
Against the backdrop of ongoing research into primary refining processes, GlobalData has identified the refinery segment as the leading adopter of digital technologies in the downstream oil and gas sector. AI-powered tools are leading digital progress by providing increased productivity and profitability.
Refiners across the globe are facing the challenge of achieving consistent quality yields and with the introduction of new feedstocks and distillation methods, real-time analysis and predictive maintenance is essential.
In recent years, AI technology has expanded to identify inefficiencies within operations and deliver actionable data on the lifecycles of existing assets in a refinery. These solutions can also optimise settings for key variables such as pressure, temperature and feedstock composition.
Investing in AI prediction models offers a significant return on investment, as digitised refineries are better placed to avoid the financial losses incurred from operational downtime. Predictive maintenance also facilitates best inventory practices for spare equipment.
AI-driven demand forecasting can be integrated to mitigate potential feedstock shortages, which combined with co-processing, means refiners can adjust to supply chain issues before they impact operations.
Refineries can be at different stages in digital maturity, thus requiring a site-specific strategy.
Gavin John Lockyer, CEO of Arafura Resources
GlobalData identifies Saudi Aramco’s 40-year-old Yanbu refinery as a mark of progress in refinery digitisation. As a significant point in Saudi Arabia’s fuel supply chain, Yanbu has been updated with AI-powered applications to reduce the fuel gas consumption of the processing units. According to the company, greenhouse gas emissions were minimised by 14%, demonstrating the additional environmental benefits AI can bring to an advanced refinery.
A report by industrial equipment supplier Emerson confirms that “for a large refinery with over 10,000 process inputs, a digital solution such as AI could save 16,000 hours per year for instrument and valve maintenance.”
The author of the report, AgileOps Alarm Management business development lead Tim Olsen, tells Offshore Technology: “Refineries can be at different stages in digital maturity, thus requiring a site-specific strategy. Understanding where a processing facility currently is and where it needs and wants to go is an important step in creating a digital transformation roadmap.”
Olsen adds that collecting and historicising refinery process and asset health data should be combined with “predictive and prescriptive analytics to turn vast amounts of data into useful and timely information. This improves plant safety, operation effectiveness, and ultimately profitability.”
Tighter refining margins and product specifications are only set to increase by 2030, making adaptability a mainstay of the industry. Developments in feedstocks, distillation methods and digital solutions are key pathways for refiners to future-proof assets.