Safety
Inside the first fully automated offshore platform
The world’s first fully automated oil and gas platform has been launched in the North Sea by Norwegian energy giant Equinor. The Oseberg H cost £606m, and has no living quarters or even a toilet on it. Molly Lempriere considers whether this is the future of the industry
Credit: Øyvind Hagen / Statoil / Oseberg Field Centre
O
perations on the Norwegian Continental Shelf (NCS) are changing as oil and gas companies embrace technological advancements in an effort to take full advantage of deposits of all sizes. Recently this drive for innovation hit a new high when the Oseberg Vestflanken H platform began production. It is the first fully automated oil and gas platform, entirely unmanned and requiring only one or two maintenance visits a year.
“With Oseberg H we take a huge technological leap forward. The fully automatic, unmanned and remote-operated platform is digitalisation in practice, and I am proud of Equinor and its partners having chosen this in-house developed solution,” said Equinor’s executive vice president for technology, projects and drilling, Anders Opedal.
The platform was created using the motto “think big, build small”, and as such is designed in the simplest way possible. This is a motto that seems to have paid off, with the platform completed on-time and under-budget, launching on the 14 October 2018.
The benefits of automation, which include improving efficiency and safety, seem clear, but an entire unmanned platform prompts some concerns. So do they represent the future of the industry?
The platform: learning curves for pilot project
The platform, located 8km north-west of the Oseberg field centre, was built in just a few years. Without the need to construct many common aspects of an offshore platform, such as living quarters, construction time can be greatly reduced.
“Oseberg H is the first platform of its kind on the Norwegian Continental Shelf with no facilities, not even a toilet,” said Opedal. “The topside weighs only a good 1,000 tonnes, another example of simplification in practice. This platform only has the bare essentials.”
It has a predicted volume capacity of 110 million barrels of oil equivalent, which lies some 110m below sea level and is accessed via 11 wells. It is managed via a control centre in the middle of the oil field, and will rarely have any personnel aboard.
Oseberg H is the first platform of its kind on the Norwegian Continental Shelf with no facilities
Oseberg Vestflanken H is a pilot project, and as such there were learning curves along the way. “The main challenges have been to develop a new profitable unmanned concept for the NCS and execute it on a tight schedule,” says Equinor spokesperson Eskil Eriksen.
But Oseberg Vestflanken H managed to come in under-budget, costing just NOK6.5bn, 20% less than expected. This will ensure that its production over the next 22 years is more economical, predicted to be below $20 per barrel.
“Oseberg H is a pilot and our first unmanned platform. We are further developing the concept and believe that the next version will be even more competitive,” said Opedal.
Ensuring safety in both the cyber and real world
The notion of fully automated platforms calls into question various aspects of safety. As with any industry embracing the third industrial revolution, cybersecurity is paramount to its success. Already Norwegian intelligence authorities have warned of threats to the oil and gas industry in particular.
“Properly securing our digital infrastructure is crucial for the safety of our employees and our installations,” explains Eriksen. “The company has a holistic approach to managing security risks where physical security, personnel security and cyber and information security follows the same security risk management process.
“Equinor manages the cyber and information security risk with focus on three key areas. Governance and policies, based on international cyber and information security standards, decides the requirements and the expected security level in the company. Technologies are implemented to support the requirements and cyber security and information security training is provided to employees to ensure awareness in the organisation.”
Properly securing our digital infrastructure is crucial for the safety of our employees and our installations
By being unmanned, human safety is improved, keeping workers far from any potential hazards. However, the physical safety of operation must still remain secured to ensure environmental safety. In the event of a malfunction, for example, being unmanned could increase the time it takes for maintenance to be undertaken.
“The Oseberg Vestflanken concept has been developed without compromising on safety,” says Eriksen. “The platform is remotely controlled from the control room on Oseberg field centre 8km away from Oseberg Vestflanken. In case of incidents the control room will take necessary actions to ensure safety on the platform. This process is very similar to the operating of remotely operated subsea wells and installations done by the industry for decades.”
Using established technologies, Equinor hopes to be able to monitor every aspect of the platform, and act when a potential leak is identified.
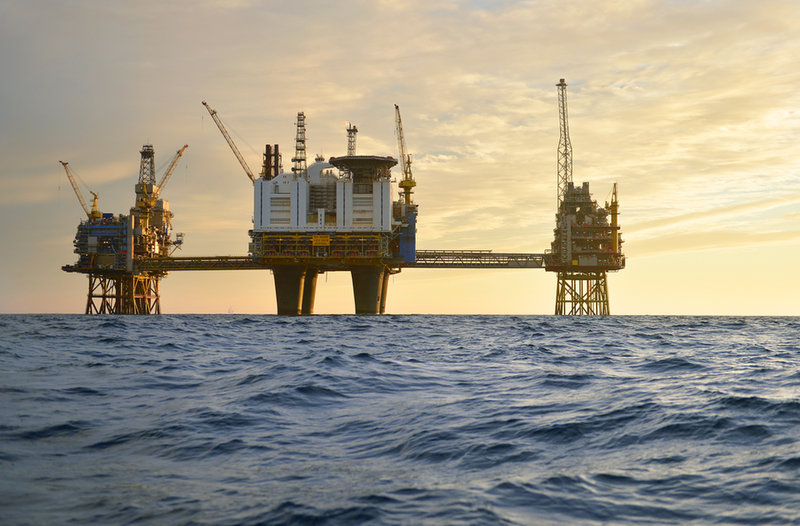
Credit: Harald Pettersen / Statoil / Oseberg Field Centre
Is automation taking over?
As industries shift to automation, many people will lose their jobs. In a recent report, McKinsey predicted that between 75 million and 375 million people around the world will need to change their job and/or acquire new skills by 2030 as positions are taken over by automation.
The oil and gas industry’s employment levels have already suffered in recent years, following price crashes and technological developments. Projects like Oseberg Vestflanken H may therefore come as a concern to oil and gas workers, as its success could signal the beginning of the end for large crews working on offshore platforms.
But according to Eriksen, this is a concern without foundation. “Oseberg Vestflanken demonstrates that new concepts provide competitive alternatives in developing smaller discoveries,” he says. “Unmanned concepts can contribute to make discoveries near existing infrastructure more profitable and can extend field life and activity level on the big existing fields.”
Unmanned production platforms have a potential to increase revenue, improve safety, reduce costs and carbon emissions
Equiror is not looking to Oseberg Vestflanken H as the new standard for all its platforms. But instead, the company sees it as a new opportunity to tap smaller discoveries that it would not necessarily have pursued in the past.
“Unmanned production platforms have a potential to increase revenue, improve safety, reduce costs and carbon emissions,” says Eriksen. “We have identified potential of reducing CAPEX by 30%, OPEX by 50%, compared to a traditional concept.”